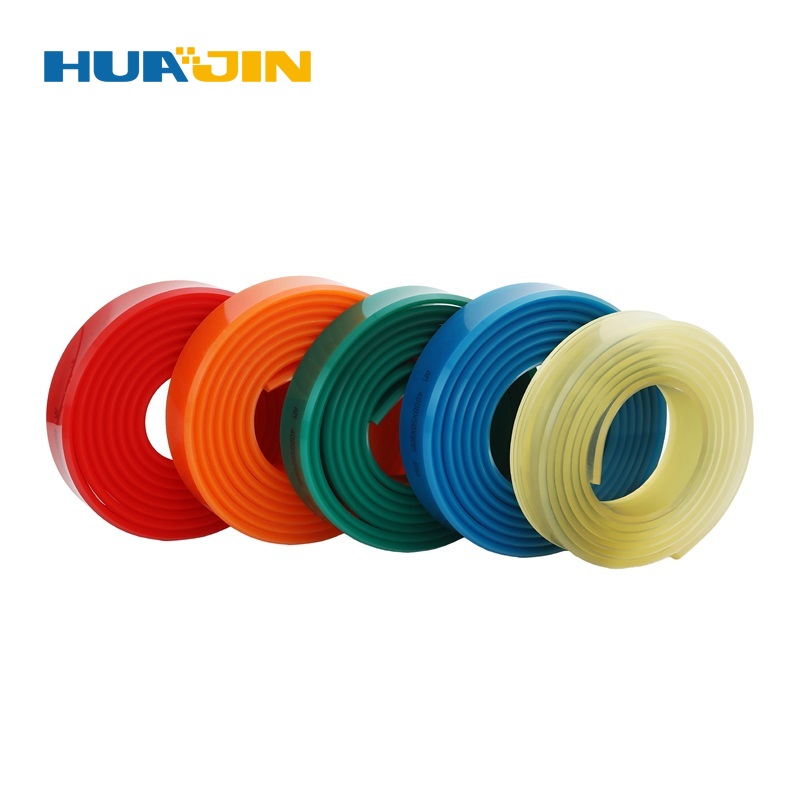
1). Transfer the ink through the screen to the substrate;
2). scrape off excess ink on the screen;
3). Keep the wire Mesh in contact with the substrate;
4). Can print different shapes of substrates.
How to choose a screen printing squeegee blade?
1).Screen Printing Squeegee Blades hardness: The squeegee is usually made of polyurethane, and the hardness of the squeegee is measured by a hardness tester. The hardness, size and blade shape of the squeegee determine the flexibility, flexibility and pressure of the squeegee blades. Hardness ranges from 55 degrees to 90 degrees (Shore A). Hardness values were measured using a Shore A durometer. 55A-65A is a low-hard squeegee, 66A-75A is medium-hard, and over 75A is high-hard.
The high-hardness screen-printing squeegee blades is very beneficial for the first three functions of the squeegee, which pushes the ink into the screen and transfers the ink from the fine stencil to the substrate, keeping the wire in contact with the substrate. The only defect of high hardness squeegee is that it can not meet the printing of different shape substrates, and the quality of screen printing squeegee is also high when printing rough surface and uneven surface.
2).Screen Printing Squeegee Blades effective width: refers to the Screen printing squeegee into the aluminum handle, the width of the strip from the aluminum Screen Printing Squeegee Blades. This width is important and determines the degree of curvature of the squeegee under pressure. The degree of curvature is the cube of the effective width.
The Screen Printing Squeegee Blades bend causes two changes: the angle between the squeegee and the screen changes; the printing pressure transmitted to the substrate is reduced. For example, the scraping rubber is compared to a set of springs. When the spring is forced at a certain angle, the spring begins to bend and the transmitted force becomes smaller and smaller. The offset printing angle is reduced, the printing pressure is insufficient, and the printing effect is not satisfactory. The printing angle is small, the printing pressure is reduced, the amount of ink is large, and the ink layer is thickened. (In this case, the printing operator will increase the printing pressure, the screen printing squeegee curvature will increase, and the obtained ink layer is still not ideal. The solution is to increase the hardness of the squeegee and increase the squeegee angle.) This is the silk. The effective width of the screen printing squeegee affects the four functions of the squeegee.
Usually the effective width of the Screen Printing Squeegee Blades is between 20MM and 30MM. The selection of the optimum effective width is based on the flatness of the substrate, the resolution of the screen image and other printing parameters such as the squeegee angle, speed and ink type. When printing a high-resolution image on a flat/smooth substrate, the effective width is small (less than 20 mm), high hardness, and fast printing with a suitable ink. On uneven and rough substrates, the effective width should be increased (sometimes greater than 30MM), the hardness should be reduced, and the low-hardness squeegee blades should be poorly adaptable, and should not be excessively bent. It is also possible to use a three-layer Screen Printing Squeegee Blades or double layer with soft sides. scratch. Generally, the effective width is increased, the printing speed is lowered, and the printing angle is increased.