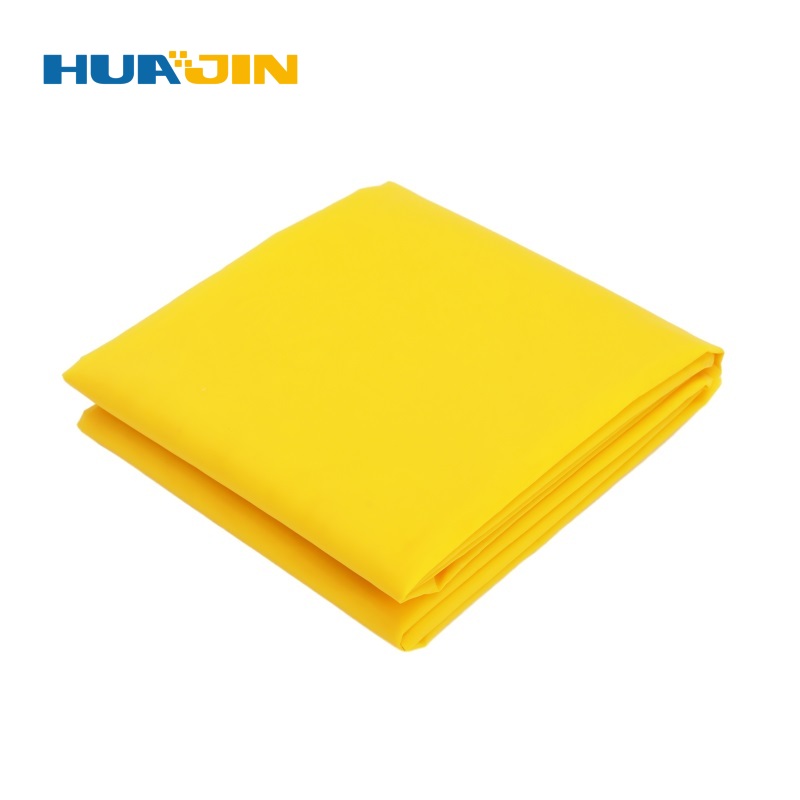
2. Try not to use soybean oil-based ink in the printing process, because soybean oil is a semi-dry (slow) oil, so it is not easy to dry when printing on paper with a dense surface.
3. The printing environment should control the pH value of the fountain solution in the range of 4.0 to 5.0. The higher the acidity (the lower the PH value), the slower the ink drying process.
4. When printing a large area of solid ground, use a varnish containing a desiccant or a transparent size for overprinting.
5. Use the recommended amount of desiccant for the ink being used. Too much desiccant will plasticize the ink, making it not dry.
6. Mixing additional desiccant in the fountain solution can improve the drying performance of the ink. GrafOSiec is an example of an additional desiccant, which can be added in an amount of 1% to 3%.
7. Make the paper stack lower at the delivery end of the printing press.
8. Use large particles of dust to help separate the printed paper and allow more oxygen to enter and react with oil and resin.
9. Let the supplier increase the strength of the ink, so that it can be printed with a thinner ink layer, which can be fixed and dried more easily.
10. Because the temperature of the printing press or paper may be too low and will delay the drying of the ink, pre-treat the paper before printing.
In short, to control the drying speed of pad printing ink, the best solution is to reach an agreement with the ink supplier, what you want to print, and what kind of ink the other party needs to provide. After choosing the right ink, you can master the points that should be paid attention to from the details to prevent the slightest failure. The oxidation rate can be increased by incorporating more oil or alkyd resin in the catalyst, or by the use of completely dry materials, such as linseed oil or tung oil, instead of semi-dry oil, such as soybean oil. Some ink drying problems are the result of improper carriers, which lead to low oxidation processes or lack of available catalysts.