1. The choice of screen frame material Generally, hard alloy aluminum square tube profiles such as LY12 and LF2 are used, and the size is 20mm wide and 20mm thick. The four corners are processed by argon arc welding or riveting. The metal frame has high precision and stable dimensions.
2. Selection of screen material At present, nylon Mesh and polyester Mesh are the most commonly used. Nylon wire Mesh has poor heat resistance, and is easy to produce thermoplastic deformation after being heated, which makes the tension uneven and affects the quality of screen printing. It is not suitable for high temperature baking for the production of bonded stretch screens or screen templates. Polyester Mesh has good heat resistance, stable dimensions, and the pattern does not change greatly due to changes in temperature and humidity. In order to ensure the accuracy of screen printing graphics, it is best to use monofilament polyester screen. At the same time, you should choose a screen with a higher Mesh number, a finer diameter, and a smaller Mesh. The color of the screen should be yellow or brown to prevent vignetting. Three. Stretch the net It is best to use a pneumatic stretcher. The quality requirements for stretched nets are as follows:
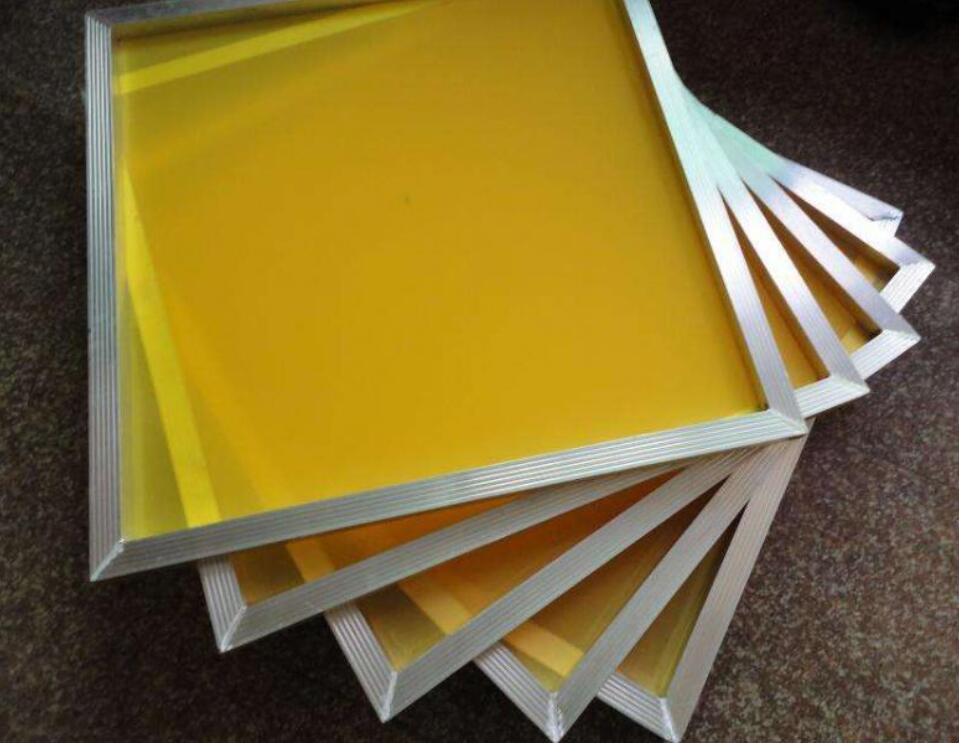
1. The tension of the stretched net is appropriate and even (1) When using a pneumatic stretcher, you must let it stand for 3-6 hours before applying the stretcher; (2) The stretched net should be placed for at least 24 hours, especially for large-sized or machine-printed nets, to ensure equal stress at all points and prevent deformation. The higher the Mesh, the longer the storage time is required, generally 2-3 days are appropriate. After placing the screen, the tension of the screen is stable, and the stresses of the name points are equal to ensure that the screen is not deformed and not easily damaged.
2. Keep the warp and weft Meshes vertical 3. Prevent slack Four. Screen template making process At present, the most commonly used method is the direct method to make screen templates. In this production process, attention should be paid to the appropriate thickness of the sizing coating, uniform sizing, and strict control of drying, exposure, development and other links to obtain high-quality screen templates.