During the thermal transfer process, the protective layer and the pattern layer are separated from the polyester substrate by the combined action of heat and pressure, and the entire decorative layer is permanently glued to the substrate by a hot-melt adhesive.
The heat transfer film is composed of a polyethylene film printed with a wood grain decorative layer as a backing paper, and the surface is coated with a protective layer, a background layer, a release layer and a hot melt adhesive layer.
By heating a high-temperature silicon roller, temperature and pressure are applied to the transfer foil, so that the transfer layer composed of decorative wood grain printing layer, surface protection layer, and base color layer is separated from polyethylene and transferred to the surface of wood-based panels or furniture parts Above, the decorative surface pattern is formed, and the surface has excellent properties such as wear resistance, heat resistance, light resistance, novel and beautiful patterns, stable color tone, and is a widely used decorative material.
The heat transfer film has unique properties. In order to obtain the ideal hot stamping effect, the best temperature, pressure and speed must be strictly controlled. There are three strict process parameters:
1. Determination of temperature: when the temperature is too low, the hot stamping will not be able to be applied or the hot stamping will not be strong, and the imprint will be blurred; will bubble. To determine the best hot stamping temperature should consider the following factors: pressure, speed, area, room temperature and so on. The hot stamping temperature generally ranges from 140°C to 180°C. Once the optimum temperature is determined, it should be kept constant, and the temperature difference should fluctuate within ±2°C.
2. Determination of pressure: The hot stamping pressure is generally 4-6 kg/cm2. If the pressure is too small, the hot stamping film cannot adhere to the substrate, which reduces the fastness; if the pressure is too large, the compression
deformation of the substrate will increase, resulting in deformation of the pattern and thinning of the printed layer.
When hot stamping complex and uneven products, it is necessary to pay more attention to the uniformity of each pressure point, and the pressure angle between the hot stamping wheel and the substrate is required to be higher.
3. Determination of speed: It should be determined according to the hot stamping area, and the power of heating temperature should be considered at the same time. Generally, the speed is first, then the pressure is determined, and finally, the temperature is determined.
The heat transfer film should be handled with care, straight and vertical, not horizontally; it should not be placed near the heat source and must be kept away from the heat source, generally stored at 25 °C;
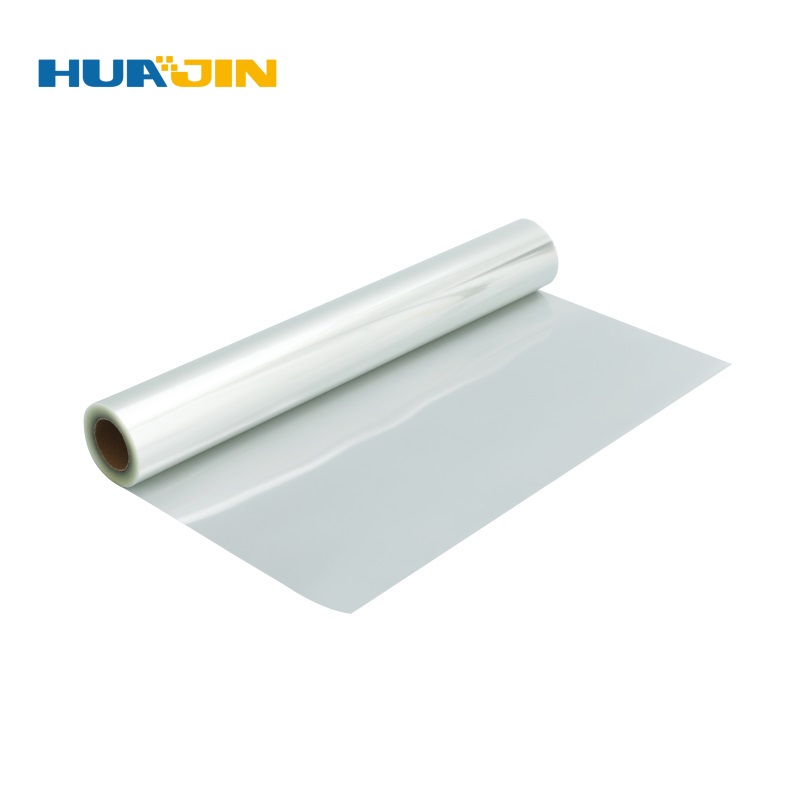